It is anything but a random choice. Indeed, to better understand it, we had to delve into the design methodology of the machine. By digging a little deeper into the documentation, we realize that the Micro5 was well thought out from the start by HE-ARC's engineers. All of this, focusing on a challenge for greater efficiency. In the end, they obtained a machine that meets objectives in terms of energy consumption, precision and dynamics, of which the 5 proved to be a founding element.
Translated with
Desired size (ratio)
Above all, the Micro5 was a project undertaken in response to a real market need. Reducing considerably the size of CNC machines has become an ambition following a logic of field. By the state of the art in the engineering field, a postulate stipulates that ideally the machine should be adapted to the size of the part it machines. For a long time now, however, there have been bulky machines in precision manufacturing, which reduce the capacity of a machine park. What we want is to make custom-built machines.Thus, for the design of the Micro5, the first characteristic that had to be defined was the maximum size of the part to be machined. Initially, the idea was in any case to create a machine for the production of watch parts. Therefore, the dimension chosen was to start with a cube of 50mm on each side. Then, it is according to the machining process and the objective described above that the choice of the size of the axis structure was made. It emerged that the Micro5 was going to be defined by an ideal ratio of 5:1 with the part it machines. This translates into an axis structure of 250mm.
Translated with www.DeepL.com/Translator (free version)
Architecture selected
Continuing with the research work, we had to imagine the most suitable structure for our Micro5. To do this, the reflection was done around the notion of the optimal stress loop. Indeed, this is what characterizes the ability of a machine to be rigid, which is essential to its performance. The certainty is that an optimal force loop must be as small and circular as possible.In addition, several aspects must be taken into consideration, such as what can be achieved by having inclined planes, rotary axes and a compact structure. Certain other conditions, such as the dynamic behavior of the moving masses, the symmetry of the structures or even ergonomics that facilitate machine protection, were also important. All these conditions were finally found around the number 5 in the definition of the machine skeleton. Divided into 5 main blocks, the machine then comprises: a fixed frame, an X frame, a Y frame, a Z frame and a cradle (composed of axes B and C).
Weight
After talking about size and structure, the footprint of a machine can also be defined by its weight. If an industrial machine is not necessarily intended to move too much, it may occasionally be useful to move it, if only for maintenance purposes.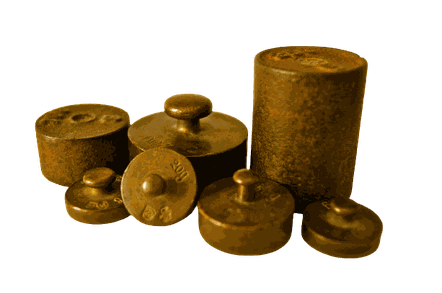
Once again, the number 5 highlights the attributes of the Micro5 perfectly. With all components in place, the Micro5 weighs almost 500 kilos, which seems completely derisory compared to the 2.5 tons average weight of conventional machine tools. The difference is quite clear, the Micro5 takes advantage of a weight 5 times less than a conventional machine tool.
Consumption
The Micro5 has also achieved another of its original goals, which is to reduce energy consumption by significantly reducing weight.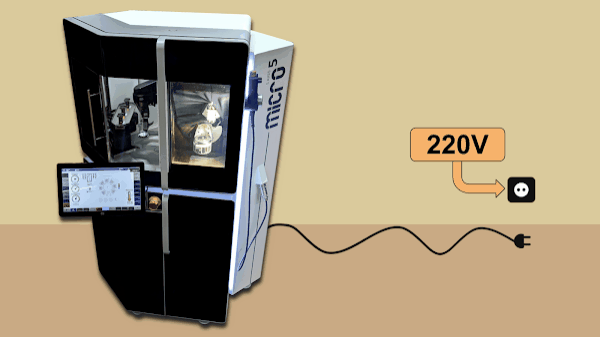
Indeed, the development of the machine has considered structures that are as light as possible. Thus, there is no need to oversize the motors (energy efficiency). While other machines with the same function on the market consume up to 25 kilowatts, the Micro5 consumes only 50 watts. Here, the number 5 does not quite represent the existing gap. However, a multiple of 5 is still relevant, because the calculated power consumption is 50 times lower than that of conventional machine tools.
Why the 5?