Maintenance
Completed
Regular inspection
Regular inspection
It is important to carry out periodic inspections to check the condition of the machine's various components.
The different lubrication points are listed in the document "M353-Maintenance_21.03.19".
The type of grease and the lubrication quantity and frequency are also indicated.
CAUTION
Regularly check the condition of the protective fabric in the machining area! If it appears damaged, stop use immediately and contact MECATIS.
Micro5 maintenance
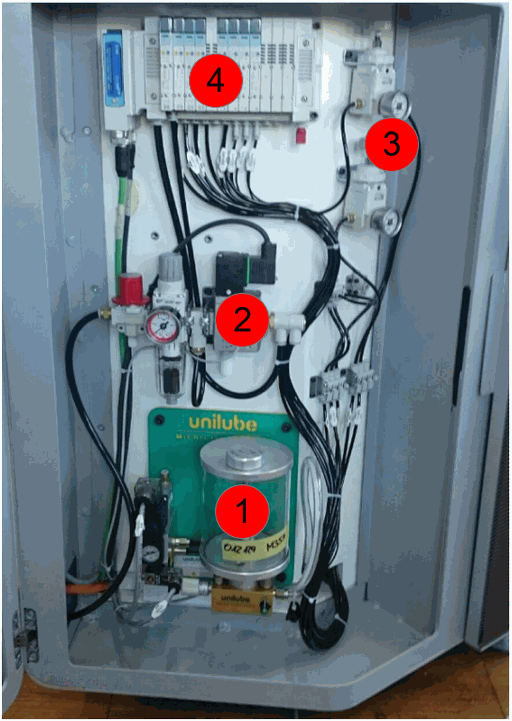
Pneumatic cabinet
1) Microlubrication
2) Air treatment
3) Spindle pressure adjustment
4) Solenoid valves
Microlubrication
Filling: max 1.5L
Unilube 9107: Gold, brass, aluminum (jewelry material)
Unilube 2032: Stainless steel, steel (relatively hard material)
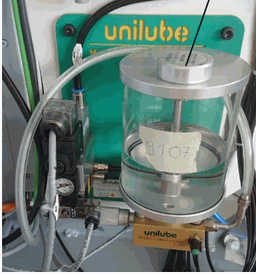
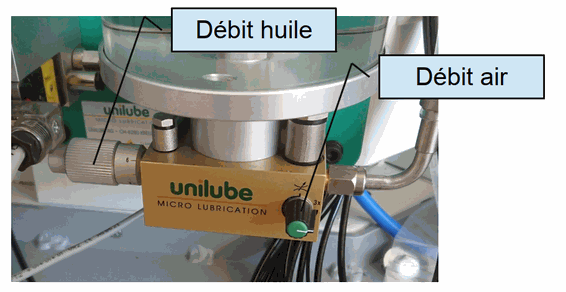
Settings
Air treatment
1) Air inlet lock
2) Pressure controller and filter
3) Discharge valve
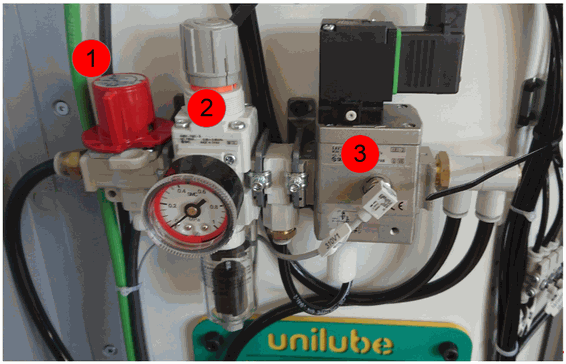
Machine lubrication
MV rail
Supplier: Klüber
Type: Klüberplex BE 31-102 or equivalent
Brush lubrication every ~400 hours of operation depending on the condition of the rails following inspection
Ballscrew
Supplier: Klüber
Type: ISOFLEX NCA 15 or equivalent
Brush lubrication every ~400 hours of operation depending on the condition of the screws after visual inspection
Scara lubrication
Z-rail
Supplier: Klüber
Type: Klüberplex BE 31-102 or equivalent
Brush lubrication every ~400 hours of operation depending on the condition of the rail following inspection
Ballscrew
Supplier: Klüber
Type: ISOFLEX NCA 15 or equivalent
Brush lubrication every ~400 hours of operation depending on the condition of the screws after visual inspection
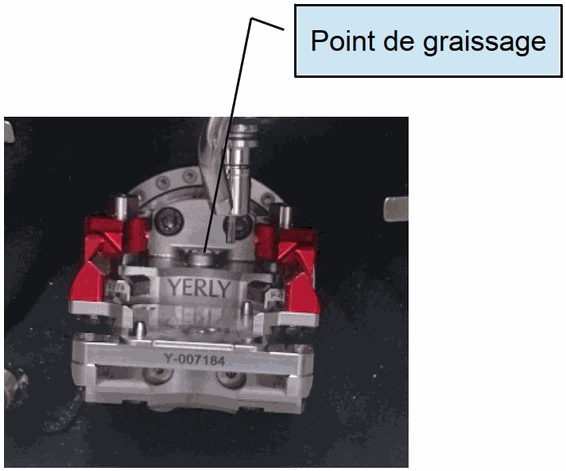
Top/bottom
Supplier: Klüber
Type: Microlube GBU-Y 131 or equivalent
Lubrication every 6 months of use..
Be careful not to add too much grease, as this could jam the device
Clean the machining area
1) Brush and vacuum the fabric and the area under the chip tray.
2) Remove the probe storage cover to check for chip accumulation. Clean with a brush and vacuum if necessary
3) Regularly clean the bottom guide rail of the partition

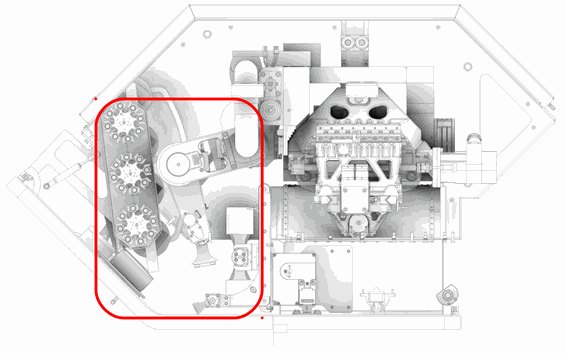
Clean the loading area
Brush and vacuum the loading area.
Beware!
Never use compressed air to blow chips into this area! There is a risk that they could settle on the screws and rails of the SCARA and the machine!
There are no comments for now.