Manual
Completed
Initialization (reset)
Initialization (reset)
The system can only be switched from the stopped state to the ready state after it has been initialized. This method meets the standards, prevents unexpected movement at reactivation and ensures that the system can only be activated deliberately by the operator.
Initialization is only possible if:
The emergency stops are triggered
The doors are closed and the interlocks are active
The motor drives do not report any errors
The feeds are set > 0%.
The extinguishing system has not been activated (option)
Before initializing the system, it is important to ensure that all safety devices are in place and that the machine can be safely activated: tools, fixtures, etc.
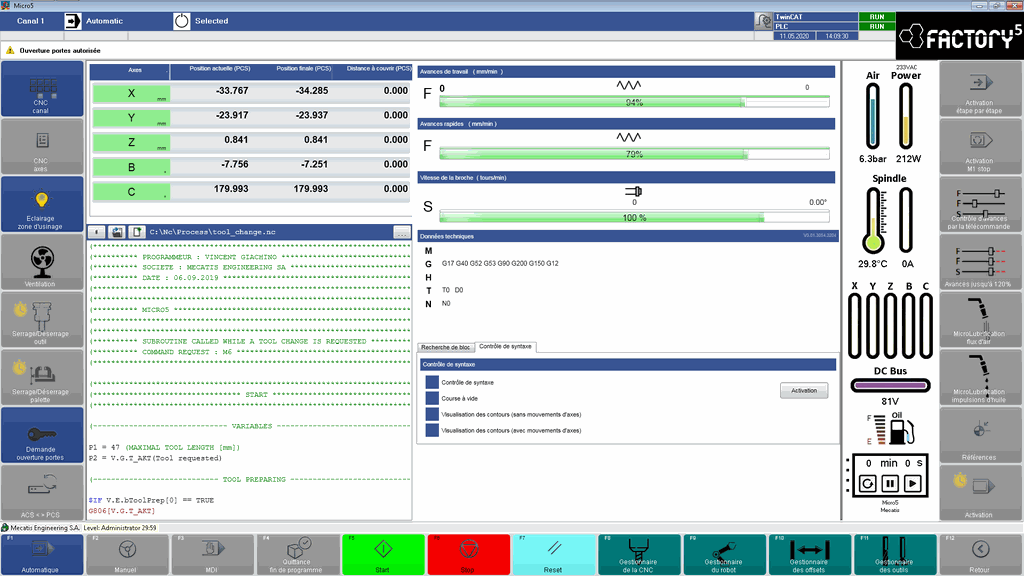
Once the system has been initialized, the following is possible (system status: stopped, initialized):
After 2 seconds: Open the main door and the magazine gate*
After 2 seconds: Open the door to the recovery zone under the machining area (if locking option)
Activate the drives of the CNC part and the SCARA
* provided that the door opening authorization is activated on the screen
Once the system is in its initial state (energy supplies), it is possible to take to take the references of the CNC axes abd the SCARA homing.
Conditions blocking initialization of the Micro5:
The following points prevent the machine from initializing and switching from a stop mode to an operating mode (manual or automatic). The cause must be eliminated and the system reinitialized (Reset) in order to use the Micro5.
Safety
Emergency stop(s) pressed
Door(s) open)
Partition locked (open/closed) during an automatic movement request
Power supply
Faulty 24 VDC power supply
Motor drives
Triamec drive faulty (power supply or logic)
Maxon drive faulty (power supply or logic))
Components (sensors)
Air pressure (machine inlet) below 4 bar
Spindle temperature above 55 °C
CNC modes
Turning mode without having activated the option
CNC axis in motion with loose pallet
Spindle turns without tools
Feeds set to 0 %
Tool breakage (optional)
Tool broken
CNC/Robot
CNC or robot not referenced or in manual model
Tool detected in spindle when no tool is indicated
Tool not detected in spindle when a tool is indicated
Probe in spindle during tool change
Error during tool change (tool not found in the magazine, tool cannot be inserted or removed, operator stop, time to perform the sequences exceeded)
Error during disk change (all disks complete during unloading, disk pick-up or set down not possible, operator stop, time to perform the sequences exceeded)
Error during pallet change (pallet cannot be inserted or removed, operator stop, time to perform the sequences exceeded)
Error during probe loading/unloading (tool detected during probe loading, probe not in spindle during probe unloading, probe cannot be inserted or removed, operator stop, time to perform the sequences exceeded)
CNC crash
Robot crash
ISO code (consistency))
CNC axis/axes out of stroke
Tool requested in automatic mode >47 mm height (with tool holder)
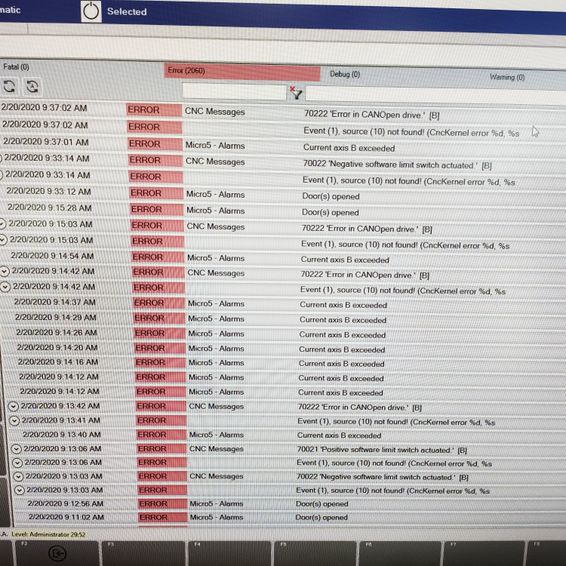
Detailed view of errors
The error detailed view lists all errors and their details: date and time, status, alarm group and alarm text.
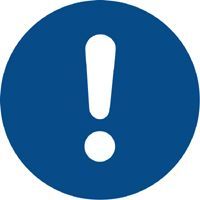
Verification of data consistency
Always check that the tool number and pallet number physically present on the Micro5 correspond to those displayed on the interface.
There are two possible scenarios depending on the version of the Micro5 software:
Software versions before 25.06.2020, 13:38 -->|
The tool in the spindle when the machine is switched off is lost; the tool number must be entered manually when switching on.
In MDI mode, enter the tool number in the program entry section and start.
|-->Software versions from and including 25.06.2020, 13:38
The tool in the spindle when the machine is switched off is stored. When the Micro5 is switched on, the tool stored when the machine is switched off is automatically transferred to the interface when the reference is taken. Tools should therefore not be manually changed before a homing operation has been performed.
There are no comments for now.